Early history
The first documented development of 3D Printing can be traced back to a Japanese fellow called Hideo Kodama in the early 1980s in Japan. Hideo was trying to find a way to develop a rapid prototyping system. Kodama came up with a layer upon layer approach for manufacturing, using a light-sensitive resin hardened by UV light.
A few years later, French researchers were also seeking to create a rapid prototyping machine. Unlike Kodama, they tried turning liquid monomers into solids using a laser.
However, neither of them filed for patents, but both are credited with coming up with the system of 3D Printing.
First Commercial 3D Printer
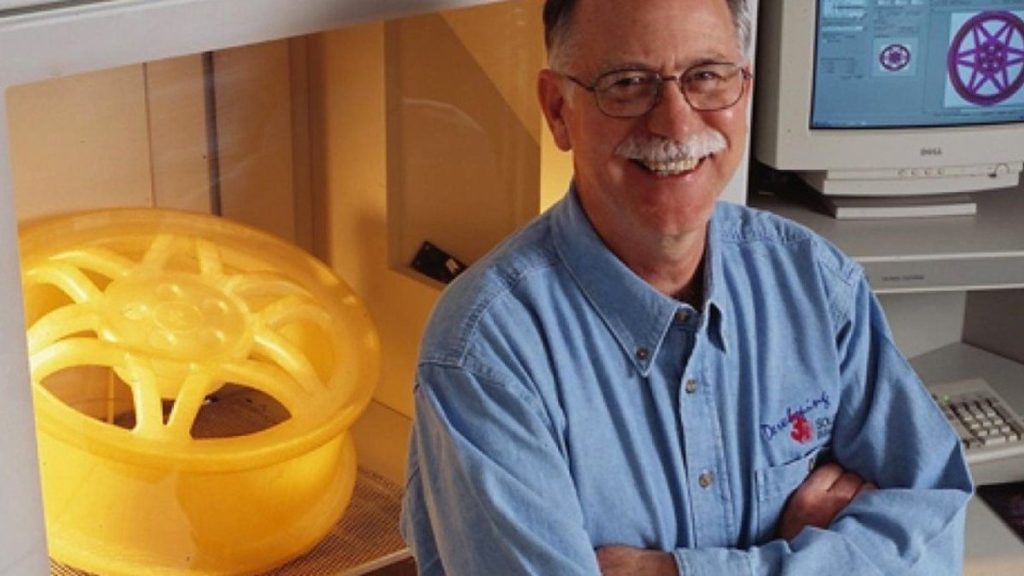
Charles “Chuck” Hull filed the first patent for Stereolithography (SLA); Chuck was an American furniture builder who was frustrated with not being able to make custom parts easily.
To solve this problem, he developed a system for creating 3D models by curing light-sensitive resin layer by layer. He was inspired to come up with the idea when he was using UV light to harden tabletop coatings.
In 1986 Chuck submitted his patent application for the technology, and not long after founded the 3D Systems Corporation in 1988.
Subsequently, the first commercial SLA 3D printer, “the SLA-1,” was released shortly after in 1988.
All 3D printed models contain layers; however, depending on what process you use, the visibility of these layers differs.
SLA offers the highest level of resolution to 3D models, with parts almost being indistinguishable from Injection moulding, which can even allow for optic lenses to be printed.
At 3D Printing Dublin, we offer FDM and SLA 3D printing.
Development of SLS 3D Printers
Following closely on the heels of 3D systems, Carl Deckard at the University of Texas filed a Patent for Selective Laser Sintering in 1988.
SLS uses a laser to fuse powder into solid objects. Unlike any other type of 3D Printing, it doesn’t require any support as the powder around the object acts as a support (supports are tiny trusses used to support overhangs in models).
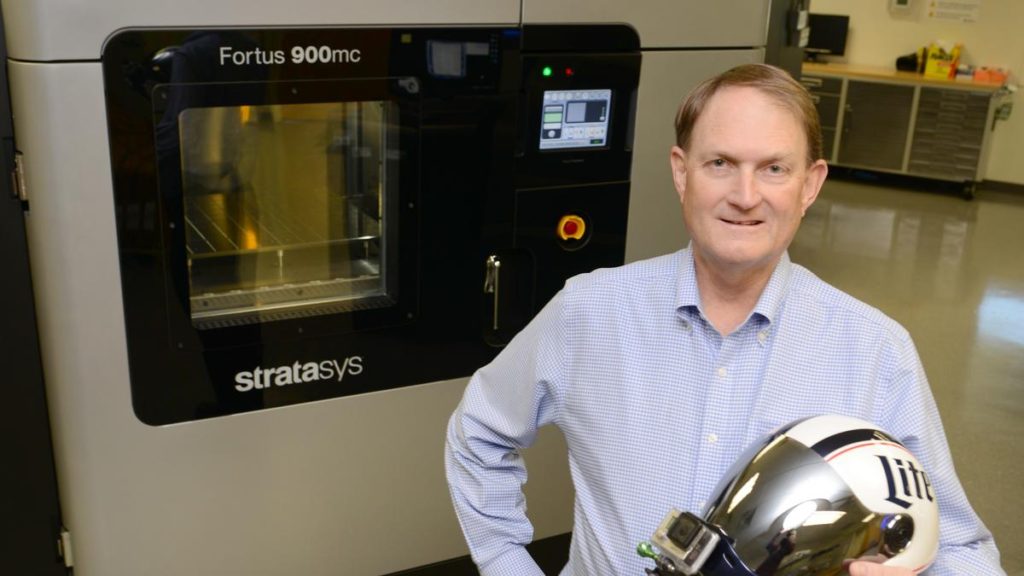
Development of FDM 3D Printers
Scott Crump first developed Fused Deposition Modelling in 1988. Scott Crump went on to found one of the big players of 3D Printing, “Stratasys”.
FDM differs from SLA and SLS in that rather than using light to harden or fuse liquid and powder; it employs the use of melting plastic filament and extruding it through a heated nozzle in thin layers to build up a model.
FDM has become the most popular form of 3D Printing due to its simplicity and cost-effectiveness.
After Scott Crump’s patent for FDM expired in 2008, a tsunami of independent companies sprung up and started making FDM 3D printers.
1990-2010: Growth
During this time, CAD tools became more widely available, allowing people to make 3D models on their computers. Giving people the tools to design essentially whatever they wanted was a big step forward in 3D Printing as it meant people had things they could make on their 3D printers.
Early 3D printers were costly, and many of the final prints required extensive post processing; however, innovations and improvements came out, making 3D Printing a little better each time.
In 2005, Dr. Adrian Bowyer created the RepRap project, an open source initiative to create a 3D printer that could print parts to make another 3D printer and print other parts.
The fact that this was open source and that many of the parts were widely available meant 3D Printing was accessible to almost anyone that had a bit of time on their hands.
In 2008 the first prosthetic leg was 3D printed, which pushed 3D Printing into the mainstream spotlight and introduced the term to millions of people globally
As previously mentioned, the expiry of the 3D printing patents filed in the 80s opened the doors for innovation as the technology was available to anyone that wanted to use it.
This decreased the cost of 3D Printing and made it more available for the average Joe.
3D Printing Now
3D Printing has come in leaps and bounds from its infancy; affordability, quality and accessibility have improved massively.
The materials available to 3D Printers are almost limitless, plastics with different properties such as colour changing and flexibility, carbon fibre, metals, and even foods like chocolate and pasta.
3D printers now come in many different shapes and forms.
Some Printers can print entire houses in a matter of days, handheld 3D printers that allow artists to express their creativity and even printers that work underwater!
Although 3D Printing is widely used across many different industries, its implementation and evolution still have a long way to go.
We look forward to seeing where 3D Printing will take us!